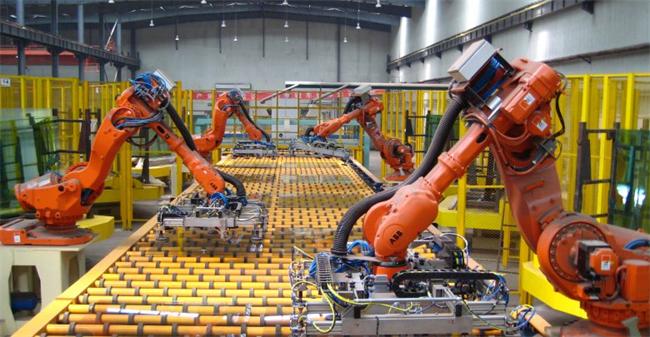
Where To Start Implementing Systems Automation: 3 Main Steps
Denying the fact that industrial robotic automation is an essential part of every successful enterprise is nonsense. This is the only way to catch up with the growing consumer demand in the age of technology. However, making the first steps towards automating your business is tiring and time-consuming. There are three steps to make to understand that automation will work for you. The final solution is to approach RIOS, which is a factory automation company that’s here for you to help.
Analyze Your Existing Processes
No matter what goods your enterprise produces, analyzing your current workflows is the key. Think of what manual vacancies you’ll no longer need and what employees should be moved to another shop floor or fired. Remember that not every process is liable to automation. RIOS Company offers the following high-end solutions that may be of use:
- ASTRIA for material handling automation
- DION for food items handling
- LUMOS for quality control
- HERMES for packing SKUs into polybags
- VULCAN for sorting, packing, and palletizing goods
Decide what factory automation components should be deployed first and start optimizing your existing workflows to achieve maximum profitability and work speed.
Automate One Process by One
Don’t rush to invest your spare capital at once since automation may not be your way to take the company to another level. Automated factory machines have an initial high cost, which is difficult to cover if your business doesn’t earn enough profit yet. It’s recommended to apply robotics to one process by one to see how your business and staff react to this novelty.
Monitor and Upgrade
Implementing automation is only the beginning of your path to reaching new manufacturing heights. Your responsibility is to constantly monitor the processes that have been recently automated. Some equipment may need an upgrade or instruction change. The same goes for the well-timed maintenance not to let any breakdowns.
Every task and workflow have a business value. It could simply be a measure of the cost in hours of workers to perform a task. If automation significantly reduces the time to perform a task, the cost of that task is also significantly reduced. Therefore, automation is credited with savings.
Similarly, automated tasks are performed the same way every time, which should reduce errors. With fewer errors, automation improves user satisfaction and reduces wasted time by solving avoidable problems.
Finally, monitoring helps determine bottlenecks within automated processes. For example, a provisioning task may fail due to insufficient server memory and succeed when the correct resources are available. Monitoring is the only objective means of measuring the value of automation and identifying problems to remediate.
Conclusion
Implementing automation is not a one-time effort. The datasets used to define an automated process, such as predefined scripts and visuals, require regular reviews and updates to keep up with changes in workflows and business needs. That is, does each automated process do what the business needs? Unfortunately, automation maintenance is often neglected or treated as an afterthought. Plan periodic reviews to review and revalidate automated processes, but don’t stop there. Infrastructure and business change are two primary drivers for maintaining automation. For example, adding new servers could increase the compute resources available for automated provisioning. Similarly, a new law might require changing the steps in an automation process to ensure regulatory compliance. To address these scenarios, maintaining automation can be linked to the organization’s change management process.